Mastering the Art of Welding: How to Prevent Undercut Welding Issues for Flawless Construction Results
Effectiveness and precision are vital in the globe of welding, where even the tiniest flaw can endanger the architectural stability of a fabricated piece. One common challenge that welders face is undercutting, a flaw that can damage a weld joint and lead to costly rework. By understanding the source of undercut welding and carrying out reliable techniques to stop it, welders can boost their craft to new degrees of quality (Preventing weld undercut). In the quest of remarkable fabrication results, mastering the art of welding to stay clear of undercut concerns is not simply an ability yet a requirement for those pursuing excellence in their job.
Understanding Undercut Welding

To protect against undercut welding, welders ought to guarantee proper welding specifications, such as adjusting the current, voltage, travel rate, and maintaining the right electrode angle. By recognizing the causes of undercut welding and implementing precautionary steps, welders can accomplish high-quality, structurally audio welds.
Root Causes Of Undercut in Welding
Understanding the variables that contribute to undercut in welding is important for welders to produce top quality, structurally sound welds. Inadequate welding existing or incorrect welding speed can additionally contribute to undercut. Understanding these reasons and applying proper welding methods can help protect against damaging problems, guaranteeing strong and sturdy welds.
Strategies to stop Undercutting

To mitigate the danger of undercutting in welding, welders can utilize calculated welding techniques intended at enhancing the top quality and honesty of the weld joints. One reliable approach is to adjust the welding parameters, such as voltage, existing, and travel speed, to make sure proper warm input and deposition. Preserving a suitable electrode angle and guaranteeing constant traveling rate can additionally aid stop undercut. Additionally, utilizing the right welding strategy for the particular joint arrangement, such as weave or stringer beads, can add to minimizing damaging. Preventing weld undercut.
Utilizing back-step welding methods and regulating the weld grain profile can additionally assist disperse heat evenly and minimize the danger of undercut. Routine inspection of the weld joint throughout and after welding, as well as carrying out quality guarantee procedures, can assist in resolving and finding damaging issues quickly.
Relevance of Correct Welding Criteria
Picking and maintaining appropriate welding parameters is essential for attaining effective welds with minimal defects. Welding specifications describe variables such as voltage, existing, travel speed, electrode angle, and securing gas circulation price that straight influence the welding process. These specifications must be carefully readjusted based upon the kind of material being bonded, its density, and the welding technique utilized.
Proper welding specifications make sure the correct amount of warm is put on melt the base metals and filler product evenly. If the parameters are set expensive, it can result in extreme heat input, causing website here burn-through, distortion, or spatter. On the various other hand, if the criteria are too reduced, incomplete blend, lack of infiltration, or undercutting might occur.
Top Quality Guarantee in Welding Operations
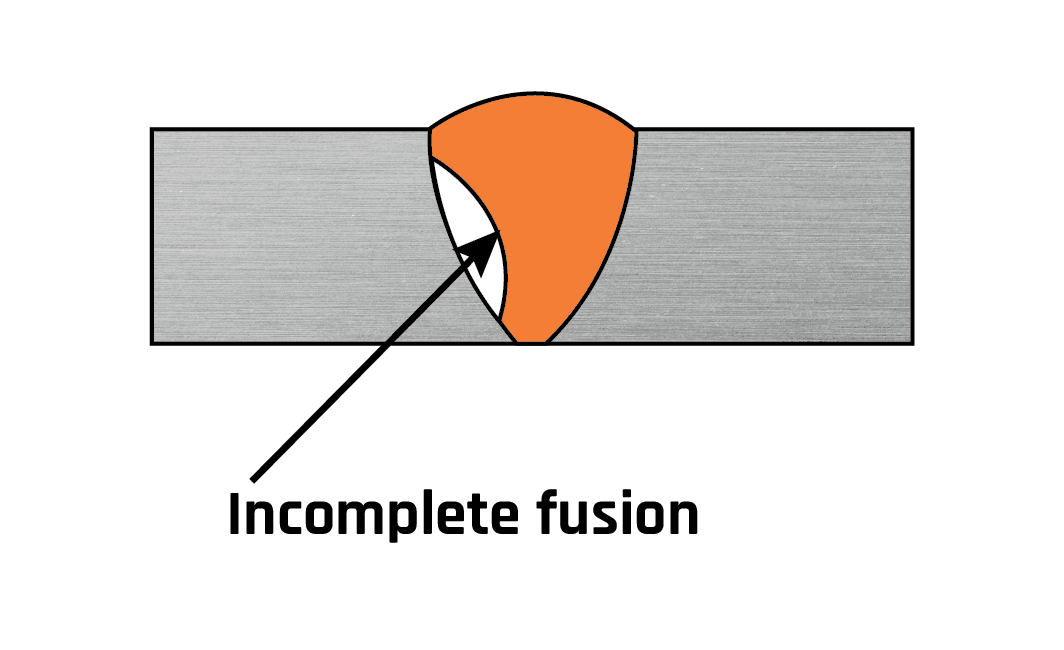
Conclusion
Finally, mastering the art of welding requires a comprehensive visit their website understanding of undercut welding, its causes, and methods to stop it. By making sure proper welding specifications and implementing quality guarantee techniques, perfect manufacture results can be attained. It is necessary for welders to continually strive for quality in their welding operations to prevent undercut problems and reference generate top quality welds.
Undercut welding, an usual defect in welding procedures, happens when the weld metal doesn't appropriately fill up the groove and leaves a groove or clinical depression along the bonded joint.To prevent undercut welding, welders must make certain appropriate welding specifications, such as adjusting the current, voltage, travel rate, and maintaining the appropriate electrode angle. Inadequate welding inaccurate or current welding speed can also add to undercut.To minimize the threat of undercutting in welding, welders can utilize critical welding methods aimed at enhancing the quality and honesty of the weld joints.In final thought, mastering the art of welding needs an extensive understanding of undercut welding, its reasons, and strategies to stop it.